This is our last post in a four-part series about building a configurable pothole for testing autonomous cars. We built the configurable pothole prototype with five independent Scotch Yoke units controlled by servo motors and an Arduino UNO. For more background, please read the previous post of this series where we discuss how to interface Scotch Yoke units with Arduino UNO and servo motors, how to setup and control configurable pothole prototype. In this post, we cover the lessons we learned by doing this project.
Lessons learned
1. We can design some tests without having access to the hardware or software product. When working on our configurable pothole project, we didn’t have any autonomous car or any sensors used for detecting potholes. We harbor no illusions – our work is not going to be used by Google or Tesla. But the exercise of building a configurable pothole was fun and enlightening. I bet the experience will make us better testers and will serve us well in the future.
2. Testing needs technical skills … just not the same technical skills as development.
3. We learned a lot about how self-driving cars work. How different combinations of sensors are used to drive the driverless cars selfly. How LIDAR sensors works and their benefits for the autonomous car.
4. While working on this project, we learned about two mechanisms (Scotch Yoke and Slider Crank Mechanism) which convert angular motion into linear motion.
5. A good fabricator is very important. Fabricators are very good consultants. They are good at providing solutions to any hardware issues e.g. friction issues, smooth operation of units, torque/hardware weight issues. We were lucky to work with Sagar Enterprise and we strongly recommend them.
6. Order some spare hardware units as fabrication of hardware units need more time. We wanted to use 6 Scotch Yoke units and we ordered exactly 6 units. Guess what? One got damaged when it was shipped. And we had to make do with 5 units and that set us back by quite a bit of time. Lesson learned – order spare hardware units.
7. Good packaging matters, even for custom made hardware units. During transportation, the possibility of damaging the things/hardware material is very high. So, making a good packing of the things/hardware unit is very important. One of our Scotch Yoke unit damaged during transportation, that may be due to the bad packing of units.
We hope you enjoyed our journey into building a configurable pothole. We realize that we do not know much. We are energetic and creative testers looking to learn. So we’d love to hear from more experienced and knowledgeable people in the comments section.
P.S.: If you are interested in other creative ways Qxf2 uses hardware for testing, we’d recommend reading about our attempts to test Fitbit’s heart rate monitor.
If you are a startup finding it hard to hire technical QA engineers, learn more about Qxf2 Services.
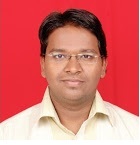
I love technology and learning new things. I explore both hardware and software. I am passionate about robotics and embedded systems which motivate me to develop my software and hardware skills. I have good knowledge of Python, Selenium, Arduino, C and hardware design. I have developed several robots and participated in robotics competitions. I am constantly exploring new test ideas and test tools for software and hardware. At Qxf2, I am working on developing hardware tools for automated tests ala Tapster. Incidentally, I created Qxf2’s first robot. Besides testing, I like playing cricket, badminton and developing embedded gadget for fun.